Notice: Undefined index: cid in /home/ogurasas/public_html/featured_product_mobile.php on line 142
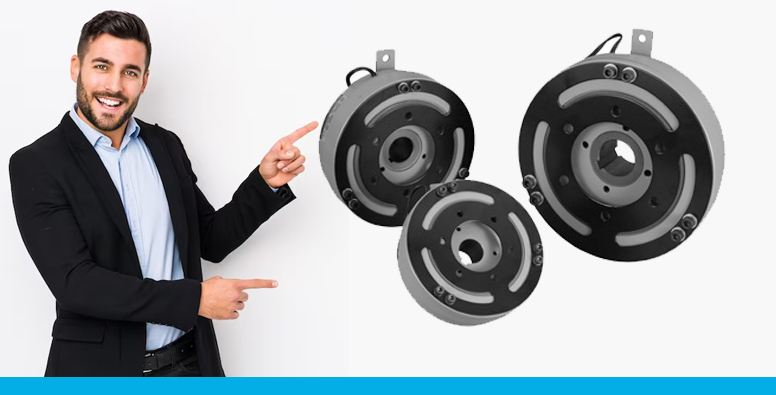
Hybrid for now, full electric for later.
Control the connection of an engine and motor on a hybrid drive system
There has been a surge in hybrid equipment designs as manufacturers and consumers realize the challenges of going full electric in one big move. For that reason, novel approaches needed to be discovered for the controlled coupling of the engine and motor. This connection requires performance, reliability, safety, operator comfort and cost effectiveness. Applications include lawn and garden equipment, construction equipment, certain low speed vehicles, boats, and more.
Electromagnetic clutches provide a solution to connect the engine to the motor/generator. There are various configurations for a hybrid machine. The engine or electric motor can run solo. They can both operate in unison. The motor can assist the engine. The engine can turn the motor to charge the onboard battery. On some hybrid designs, a solar or wind power source can be added to charge the battery as well.
The way an electromagnetic clutch works is by applying electrical current to either engage or disengage the clutch. Most clutches are power-on devices meaning that they engage when power is applied, although there are some that are naturally engaged and then released with power applied. The transfer of torque is done mechanically through friction surfaces.
Electromagnetic clutches can be bi-directional. Some have directional leaf springs which means that type of clutch can only be rated for full torque in one direction, and then torque is de-rated to run in the opposite direction. This would apply to reversing a prop on a boat, or when using the motor to assist the engine at startup, for example. There are other types of electromagnetic clutches that can run full torque in each direction if required.
Electromagnetic clutches can be controlled by either a hand operated switch or a programmed power supply. Clutches can be engaged at any speed. Because clutch wear rates are lowest at slower rpm, it is ideal to engage at slower rpm. Engaging at higher rpm will also introduce heat so the cycling rate may need to be monitored, depending on the application details.
General purpose clutches have a long history of applications in the outdoor power equipment market. The clutches come in several output varieties. The hub output is used for inline applications by mounting a flexible coupling half to it. For belt driven applications, a pulley is mounted to the hub, and some clutches are factory fitted with a particular pulley type. Some OEM customers mount a sprocket to the clutch to run a chain drive. Ogura General Purpose clutches are rated for 110 to 400 lb-ft static torque.
If full torque is required in each direction, a bi-directional clutch such as Industrial or Mobile clutch model MMC is used. These are heavy duty clutches, with torque ratings up to 1,500 lb-ft and built to withstand outdoor environments and heavy vibration. They also are easily driven by universal drive shafts, as the bolt pattern on the universal hub matches up with common drive shaft couplings. MMC clutches also have a limp home feature where the clutch can be mechanically locked in the engaged position if a problem arises out at sea or in the middle of an important job on land.
Benefits of using an Ogura mobile and general purpose clutches:
- Long life
- Safety and convenience with remote starting
- Fuel and energy savings
- Built for outdoor operation
- Many years of proven success
- Custom designs available based on minimum order quantities
- Reduced engine load on cold weather starts
- Increased operational life of driven equipment
- Lower fuel consumption
- Available with a soft start controller
- Slip detect capability
- Simple installation